Q. What kind of technologies are required to build the next generation of supersonic transport?
Ohnuki: The most essential technologies are reducing sonic booms at cruise and noise at takeoff and landing, and improving fuel efficiency by cutting aircraft weight or aerodynamic drag.
Makino: During supersonic flight, an aircraft compresses air around it and generates shock waves that are heard as an explosive sound on the ground. This is sound called a sonic boom. I actually heard the sound when the U.S. Federal Aviation Administration was measuring sonic booms caused by fighter jets. It was so loud, like the sound of a big fireworks display, that I literally felt the shock.
Ohnuki: The Concorde, the only commercial supersonic passenger aircraft, had to be discontinued due to its poor fuel efficiency and sonic booms. With this in mind, JAXA started working on new supersonic technology, to find solutions to the Concorde's problems.
By the way, did you know that supersonic technologies for fighter jets and passenger aircrafts are completely different? I'm often asked why it is so difficult to build supersonic passenger aircraft when supersonic fighter jets already exist. The major difference is that fighter jets can fly at supersonic speeds for only a few minutes, maximizing the engine thrust only when necessary, like when they have to escape from an enemy or hurry to a destination, for example. This is because mobility is of greater importance for fighter jets than weight or aerodynamic efficiency. On the other hand, supersonic passenger aircrafts have to maintain supersonic speeds for several hours, so you have to take engine efficiency, aircraft weight and aerodynamic efficiency into account. Working on commercial aircrafts, we have very different issues to resolve compared to the development of fighter jets.
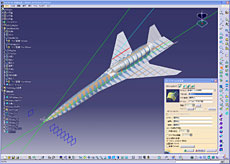
Aircraft geometry definition in CAD system.
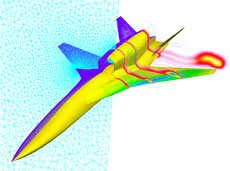
Performance evaluation of airframe with CFD analysis
Q. Could you tell us about your research, Dr. Makino?
Makino: My research focuses on aerodynamic design technology that delivers both sonic boom reduction and better aerodynamic performance at supersonic speeds. It is known that sonic booms and aircraft configuration are integrally related. For example, the intensity of a sonic boom becomes lower when the aircraft nose is designed blunt. But the problem is that a blunt nose causes greater aerodynamic drag at supersonic speeds due to a strong shock wave, and thus poor flight efficiency. So I'm trying to find a optimal aircraft configuration that can solve this paradox, using computer-aided design technology.
Q. Does JAXA have world-class technology for supersonic transport research?
Ohnuki: JAXA's world-class technology for such research is our computer simulation technology, which allows us to build and fly aircraft in virtual reality. From analyzing the propagation of sonic booms to designing aircraft to reduce their impact, we can model everything with computers. I believe that this design technology is truly world-class.
We are currently developing a computer simulation program that will estimate the aerodynamic performance and sonic booms of supersonic transport at the same time. This program can be utilized to optimize aircraft configuration by adjusting multiple variables, so that the design requirements are satisfied. So, for example, it will be able to find the best configuration to solve the contradictory problem mentioned earlier, where an attempt to reduce the sonic boom increases aerodynamic drag, thereby decreasing aerodynamic performance, while, conversely, better aerodynamic performance generates greater sonic booms.
This is called multi-objective design optimization, and it's a more advanced method than the inverse design methodology we developed previously. In conventional aircraft design, you first decide on an aircraft configuration, and then estimate its characteristics. With the inverse design methodology, it's the other way around: you determine the characteristics first, and then find the right configuration to match your needs. The disadvantage of the inverse design is that it requires another step - analyzing the overall performance of the resulting aircraft configuration from its characteristics. But with multi-objective design optimization, you can optimize the configuration by simply specifying the multiple performance aspects you'd like to improve, such as aerodynamic drag and sonic booms.
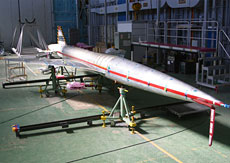
National Experimental Supersonic Transport (NEXST-1), designed with the reverse methodology
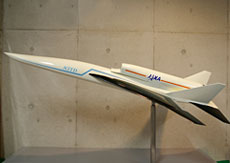
Scale model of the Silent Supersonic Technology Demonstrator
Makino: Let me give you a more specific example. Say, you decide on an aircraft configuration and test it in the computer simulation program, which gives you analysis data on airflow around the airframe. This is an example of forward problem. Alternatively, in the inverse problem, you can specify the airflow you'd like to achieve around an airframe, and the program will provide the optimal aircraft configuration. However, what we need is more than inverse engineering design; we need to take a step forward, because what we'd like to achieve is not a specific flow field but an aircraft configuration that can satisfy both performance requirements and noise criteria. Once we determine the flow field around the airframe, we have to evaluate the consequences, such as the aerodynamic drag and the sonic booms it generates. Multi-objective design optimization technology resolves all these objectives simultaneously, optimizing aircraft configuration in one step. This is the computer design technology we are developing.
Just as contradictory demands exist between sonic booms and aerodynamic performance, there is also a conflict between aerodynamics and structural dynamics. For example, from an aerodynamic point of view, the best main-wing configuration for supersonic aircraft would be razor-thin wings that can cut through the air without moving it. However, from the point of view of structural dynamics, such thin wings are out of the question, since they will bend too easily. So, in the past, we had to try different thicknesses one after another until we found the ultimate configuration. It was an extremely slow and inefficient process. That's why we decided to apply the multidisciplinary design optimization methodology, to develop a computer program that simultaneously addresses multiple issues such as aerodynamic performance and aircraft structure, for example. If you want to know how the thickness of aircraft wings impacts the aircraft structure and aerodynamics, the computer program will perform the analysis and estimate the characteristics. It can also optimize the configuration from the estimate results. Obviously, automating this process greatly improves design efficiency. We have just started applying this design optimization program to the development of a silent supersonic technology demonstrator. We're thrilled with how it is progressing.