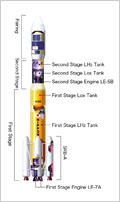
H-IIB Launch Vehicle

The H-IIB launch vehicle is a new large-scale rocket being developed jointly by JAXA and Mitsubishi Heavy Industries, Ltd (MHI). JAXA is also developing the H-II Transfer Vehicle (HTV), a spacecraft that will transport supplies, including devices, foods, and closing, to the International Space Station. The main objective of the H-IIB is to launch the HTV.
The line-up of the H-IIA and H-IIB launch vehicles will allow Japan's space program to become competitive internationally by helping Japan's private-sector aerospace industry increase the number of commercial launches. This is Japan's first attempt at public-private development of a launch vehicle. The H-IIB's launch capacity was jointly agreed upon by JAXA and Mitsubishi Heavy Industries, to accommodate both the new HTV, which is a national project, and commercial launch services.
The H-IIB adopts the design methods and components that have already been verified by flights of the H-IIA, so that we will be able to manufacture the new launch vehicle more cost-effectively, with less risk, in a shorter period of time.

First-stage cluster engine at a firing test
The most significant difference between the H-IIA and H-IIB launch vehicle is launch capacity. Because the maximum launch capacity of the H-IIA is about 12 tons to Low Earth Orbit (LEO), it cannot carry the HTV, which weighs 16.5 tons. For this reason, the launch capacity of the H-IIB was set at 16.5 tons. To achieve this, H-IIB use two first-stage H-IIA engines (LE-7A), which are clustered and loaded with 1.7 times more propellant than on the H-IIA. To achieve this improvement, the diameter of the first-stage body has been expanded to 5.2 meters from the H-IIA's 4 meters.
When injecting into the Geostationary Transfer Orbit, the H-IIB can carry a payload of up to 8 tons, versus 6 tons for the most powerful version of the H-IIA series, the H2A204. The H-IIB will be able to launch two 2- to 4- tons geostationary satellites on one flight, so its commercial potential is very high.
Using many components and technologies developed for the H-IIA has allowed us to reduce cost and risk and improve the reliability of the H-IIB. Because the HTV is the biggest spacecraft we have ever launched, the length of the H-IIB's payload fairing (a cover to protect the payload from aerial drag and external heat at ascent) has been extended from 12 meters to 15 meters, with no change to its diameter. The bigger fairing and its greater load made the skin of the second stage a little thicker, but the second stage of the H-IIB is basically the same structure as the H-IIA. Finally, the H-IIA's first-stage main engine is used for the H-IIB's first stage cluster engine, and mounting four solid rocket boosters has already been proven to be effective by the H-IIA Flight No. 11.
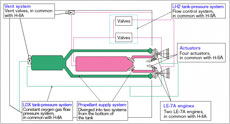
Schema of the First Stage Propulsion System

The biggest challenge in the development of the H-IIB is clustering two engines, which has never before been done in Japan. Clustering multiple engines allows us to increase the thrust. Using the large engine already developed for the H-IIA, we can reduce development time, cost and risk. However, it is important to make sure that the two clustered engines will fire and operate in perfect synch; thus very high reliability is required. To achieve this, we have come up with innovative design ideas.
One idea is for the propellant supply system, consisting of tanks, pipes and valves. The H-IIB's propellants are liquid oxygen and liquid hydrogen, the same as the H-IIA's. They are supplied separately to the two engines, through separate pipes branched at the outlet of each propellant tank. This supply system allows each engine to combust individually and stably, without being influenced by the other engine. Also the distance between the two engines is set so that gas emission from one engine does not interfere with the other.
To test the system design, we have conducted eight firing tests with the simulated first-stage propulsion system, called Battleship Firing Tests, since March 2008, at MHI's Tashiro Test Facility in Odate, Akita prefecture. With the exception of the propellant tanks, actual components - including engines and propellant pipes - were used. The walls of the propellant tanks used for the tests were thicker and tougher than the real ones, so that we could test with higher pressure as well as applying a greater range of engine inlet pressures. All results thus far have been favorable. Exhaust gas interference during engine combustion can be calculated beforehand, but you can never be certain of the accuracy before the engine firing test. Test results were within the range of our expectations. We have successfully tested the first-stage propulsion system, which is the most challenging part of the H-IIB development process.