Nippon Kayaku Co., LTD. (KAYAKU) and the Japan Aerospace Exploration Agency (JAXA) successfully developed a motor coil that can maintain its maximum power more than two times longer than a conventional model by using thermal conductive heat-resistant insulating material. Technology to extend the time duration of motor’s maximum power is imperative for the practical use of an electric aircraft.
JAXA has been engaging in research and development of an electric aircraft as one of the most promising aviation technologies for future aircraft. For an electric aircraft to efficiently take off, it is important to maintain maximum power for a brief period. However, a conventional motor cannot sustain maximum power for a long time or the coil will burn out due to the temperature increase. Thus the necessary output power was secured by using a bigger motor system, limit the operation time and maximum power of the motor, or by introducing a cooling system. Therefore, in order to realize a smaller high-performance electric aviation motor, JAXA has been seeking a coating for the motor coil that has both insulation properties and strength while promoting thermal conductivity.
On the other hand, KAYAKU, by using reactive Polyamide resin as a base, has been developing a thermal conductive heat-resistant insulating material that can be used at up to 250 degrees Celsius with high thermal conductivity and strong adhesive properties.
In a joint research collaboration that was launched in fiscal year 2011, KAYAKU applied the thermal conductive heat-resistant insulating material to the electric aviation motor coil, while JAXA tested and evaluated the motor. Consequently, a motor coil capable of doubling the time duration of maximum power with approximately 1% improvement in maximum efficiency compared with a conventional model was successfully developed.
This technology helped develop a larger power motor system, and it can also enable us to have a lighter system if we maintain the same power as that of the conventional one, thus it is expected to be applied not only to aircraft but also to large-size automobiles and various electric industrial devices that require a higher power.
(Reference)
Electric aviation motor coil
using thermal conductive heat-resistant insulating material
In a conventional motor, copper loss (electric energy loss due to electric resistance) in a coil occupies a major part of the total energy loss of the motor. The coils are packed in a part where is difficult to cool down, and electric resistance becomes larger due to the temperature increase by electricity. As a result, the electric current cannot flow smoothly and the maximum power of the motor is reduced while the coil burns out. Therefore, controlling the temperature increase of the coil has been an important challenge to maintain the maximum power of the motor. The conventional motor needs some measures such as limiting the time duration of the maximum power, making the system itself larger, or introducing a cooling system.
In the case of an electric car motor, maintaining a maximum power for 30 seconds or so is enough for practical use. On the other hand, the electric aviation motor needs to sustain maximum power for two to five minutes when an airplane is taking off from a runway. Therefore, more resistant insulation material with high radiation performance is required.
The new coating material developed by KAYAKU is based on reactive Polyamide resin, which can withstand temperatures of up to 250 degrees Celsius and possesses high thermal conductivity and adhesive properties. For processing, coating can be performed through heat treatment of 100 to 150 degrees Celsius after applying liquid precursor, which enables the adhesion of the iron core to the motor case simultaneously with coating and adhesion of the iron core to the stator, drastically decreasing the processing time.
The following diagram shows the results of performance analysis conducted by JAXA between a motor using the new material and another with a conventional insulation material. Figure 1 indicates that the time it took for the new coil to reach the temperature limit is more than two times longer than that of the conventional one. There was no change in coating after the test, thus the insulating property is secured and strong adhesiveness was maintained. Figure 2 shows that the coil temperature of each power was decreased and copper loss was reduced. As a result, maximum motor efficiency increase of about 1% was successfully achieved as shown in Table 1.
This technology is expected to be applied not only to electric aircraft but also to various electric devices that require a motor system, for example, industrial equipment that requires high power motor such as buses and trucks.
(Attachment)
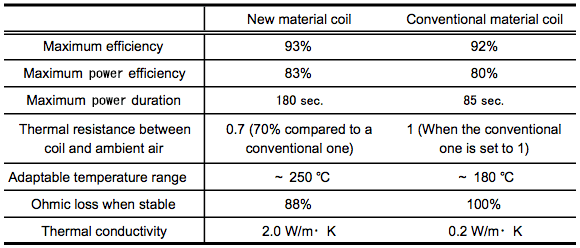
Table 1: Performance comparison between motor with newly developed coil vs. conventional one
Figure 1: Coil temperature change at maximum power
Figure 2: Coil temperature change by motor power