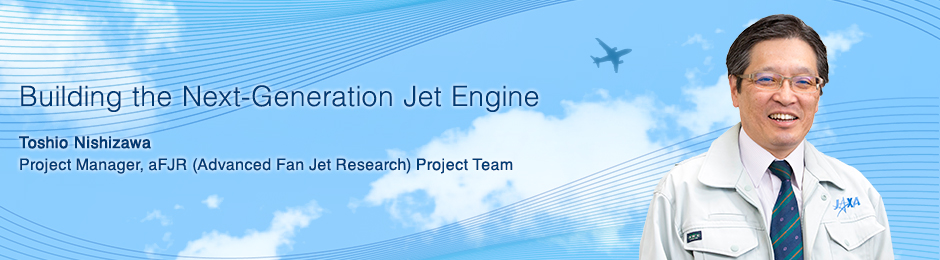
Demand for fuel-efficient, low-emission, environmentally-friendly engines is growing around the world. JAXA’s aFJR (Advanced Fan Jet Research) is a project to develop technologies that will meet this demand. We asked aFJR project manager Toshio Nishizawa about his team’s cutting-edge work.
Creating a national asset for Japan
— Could you explain how a jet engine works. How is it different from a car engine?
Both aircraft and car engines convert thermal energy, which is generated by burning fuel, to generate power. Both take in air, compress it, combust it mixed with fuel, and emit the combustion gas outside. In a car engine, these four operations intake, compression, combustion and emission are done in one chamber, while an aircraft engine uses a different chamber for each:
- A fan sucks in air.
- A part of the air is fed into a compression chamber.
- The compressed air is mixed with fuel and burned in a combustion chamber.
- The combustion gas is emitted, through a turbine, from an exhaust port.
Thus, each chamber plays a different role, and for an aircraft engine each is designed separately. This allows us to work with different manufacturers on different component technologies, and makes it easier to collaborate internationally on development. It’s difficult for a company to design and build a whole aircraft engine by itself, considering the technological and financial risks, since development is so expensive. So Japanese corporations often team up with major British and U.S. engine manufacturers.
So, for Japan to maintain its international relevance in the development of next-generation aircraft engines, it is important for us to come up with very competitive component technologies. That’s why it’s so important for the aFJR project to succeed.
— Which component technologies are you working on?
aFJR’s proposed engine
Our project is focused on high-efficiency, lightweight fan technology, and lightweight, low-pressure turbine technology. We are developing and verifying technologies for a lightweight fan with improved aerodynamic efficiency, and a lightweight, low-pressure turbine that rotates the fan. Today’s aircrafts require lower fuel consumption, reduced noise, and reduced emission of nitrogen oxides. To improve fuel efficiency, we are focusing especially on increasing the engine bypass ratio. That’s the ratio between the mass of air that flows through the engine fan but passes outside the combustion chamber, and the mass of air that is sent to the combustion chamber in the core engine. The higher the bypass ratio in other words, the greater the mass of air that flows only through the fan, not through the combustion chamber the greater the fuel efficiency and noise reduction. The bypass ratio of the engine of the latest Boeing 787 is approximately 11:1, which is quite a high for commercial jet engines, but we are aiming even higher, at 13:1.
How are we going to achieve this bypass ratio? The solution is to enlarge the diameter of the fan to increase the mass of airflow. However, a larger fan would not only be heavier itself, but would also force us to increase the diameter of the low-pressure turbine, which rotates the fan. So the overall weight would increase, which would reduce fuel efficiency. To prevent this, it is critical to make the engine components lighter than ever. Our project aims to reduce the overall engine weight by approximately 10 percent compared to referenceengines, by reducing the weight of the fan and the turbine. We also aim to increase the aerodynamic efficiency of the fan by at least 1 point.
Creating technologies for a safe, lightweight, quiet engine
— How are you going to reduce the weight?
Prototype of a hollow CFRP blade model. At left is a CAD model. Light blue indicates CFRP, and darker blue indicates the hollow center.
Prototype of an acoustic liner with a resin honeycomb structure (bottom left)
We have some ideas. First of all, fan blades can already be made from a composite material, carbon-fiber-reinforced plastic (CFRP). We are thinking of making them lighter by making them hollow. Nobody has figured out how to hollow out CFRP, so we would like to be the first to accomplish this. We are also working on reducing the weight of the metal disk that holds the rotating fan blades.
The inside of the engine cover that surrounds the fan has an acoustic liner, which reduces noise. It’s a panel with a honeycomb structure, currently made of an aluminum-based material. We are studying the possibility of using plastic instead, to reduce the weight. This also has never been done before, anywhere in the world. Also, we are looking into changing the shape of the acoustic liner to achieve greater noise absorption. Our primary goal is weight reduction, but we are aiming for noise reduction at the same time.
As for the low-pressure turbine, we are trying to reduce the weight by using ceramic-matrix composites (CMC). CMC is not only light, but also has great heat resistance. Even the latest heat-resistant alloy can withstand temperatures of only about 1,100℃, while CMC’s temperature limit is more than 1,200℃. We are working on simulations and experiments with JAXA’s Advanced Composite Research Center and Structure Research Group.
— It must be difficult to maintain durability while reducing the weight.
Thanks to the efforts of manufacturers, the strength of composite materials has greatly improved. But aircraft engines have special requirements that make it difficult to use composite materials. This is because composite materials were introduced in aviation only recently, which means there is not a lot of data available on their use. Take, for example, a bird strike a bird colliding with engine fan blades. There are regulations regarding the fan’s durability: it cannot break from a collision with a bird of up to a certain size. With metal fan blades, we have enough experience to predict how they will break, but composite materials are unpredictable because they break totally differently if there is even a slight change in the method of production. And hollowing out a composite material has never been tried before, so there is an additional technological risk. We are doing in-depth simulations under various conditions, and we hope this will allow us to predict the effects of such collisions. JAXA is known for its simulation technology, so we are confident that we can achieve a feasible design.
— Could you tell us about the current status of the project and the next steps?
Fan for aerodynamic performance test
The aFJR project started in Fiscal Year 2014. Currently, we are conducting many impact tests and aerodynamic performance tests for example, studying damage caused by solid masses striking a turbine made of CMC. Because CMC is ceramic, it can break in many different ways: for example, one part may break cleanly, while another part, where fibers are connected, may break off jaggedly. We are in the process of accumulating data on how a turbine would break depending on where it’s hit. We are going to continue verification, and are scheduled to finish the demonstration of the feasibility of the component technologies by Fiscal Year 2017.
An engine fanatic from childhood
— How did you get interested in aircraft?
I was more interested in cars, which were always around me. I was particularly interested in car engines. My father had an old car he loved to drive. Today’s cars start at the turn of a key, but that had an engine that didn’t start unless you first pulled the choke with your hand, and even then would immediately stall if you didn’t warm it up for two or three minutes. Plus, the car wouldn’t run if you forgot to occasionally take out and polish the spark plugs. It was really a high-maintenance car. Nonetheless, my father didn’t seem to mind, and in fact, rather seemed to enjoy it. Probably because I watched him from childhood, I took to fiddling around with machines myself. Then I took over his car and drove it during my four years in college. I studied aircraft engines in university, and since graduation I have been involved with engines for almost my entire career. So my life is totally dedicated to engines! (laugh)
— What is the appeal of engine research for you?
Working on a satellite, for example, is all about making a “thing.” Engines are more about experimenting to develop a specific component, which could form the basis of a lot of new technology. And therefore, I think that, for engines, you need more of a researcher’s mindset. The success of an experiment is not the end; we also look at how the experiment could have failed. We thoroughly investigate the reasons the experiment went well, and how it could go wrong, in order to understand the correlation between cause and effect. And then, once I comprehend why the experiment was a success, I can finally celebrate from the bottom of my heart.
— What is an ideal aircraft for you?
It would be a jet with little noise and improved fuel efficiency, which could take off and land even at a small airport. In Japan, people often have to travel a long way to get to a large airport that can accommodate jet flights, even though there may be a small airport much closer to home. For example, near JAXA Chofu Aerospace Center Aerodrome Branch there is Chofu Airport, but jets are not allowed to use it due to noise. If the noise from jets can be greatly reduced and it becomes possible for jets to take off on a short runway, I think the use of aircraft will grow. If people can fly easily to another city from their nearest airport, I expect that a lot more people would be traveling casually by plane.
Contributing to Japan’s aviation industry
— What is JAXA’s strength in the development of engines?
FJR710 engine developed for research. Its advanced technology was internationally recognized and incorporated into the V2500 engine, which was developed under international cooperation and commercialized.
As I mentioned earlier, JAXA is known for its simulation technology using supercomputers. We simulate the operating states of each component of an engine, such as compression and combustion, and we not only evaluate positive and negative aspects of the results, but also thoroughly investigate the causes why and how certain results were achieved. JAXA has researched and developed many engines FJR engines from 1967 to 1975, supersonic transport engines, and clean engines and has accumulated a large volume of data, which is used in our simulations. The simulation results are made available to manufacturers for product development.
— Finally, what is your vision for the future?
My primary goal is to ensure the success of the aFJR project. It is a joint project between JAXA, manufacturers and universities, so once the demonstration tests are over, it will be easier to apply the outcomes in practice. All of the technologies aFJR is trying to develop are progressive. If we can let the world know that these technologies can be applied to any design, I believe this will also promote Japan’s industrial development. So, first, I would like to see an engine built with the best of aFJR technologies, under international collaboration. Japan has previously built a jet engine, called FJR, but only for R&D purposes, and it never became a complete engine installed on an airliner. In the future I would like to see a domestic engine, and indeed an entire passenger aircraft, built with only Japanese technology.
Toshio Nishizawa, Ph.D.
Project Manager, aFJR (Advanced Fan Jet Research) Project Team, Institute of Aeronautical Technology, JAXA
Dr. Nishizawa graduated from the Department of Aeronautics at the Faculty of Engineering of the University of Tokyo in 1984, finished his master’s degree at the School of Engineering, and became an assistant at the College of Arts and Sciences in 1986. In 1990, he joined the National Aerospace Laboratory of Japan (now JAXA), and in 1994 obtained his doctorate from the University of Tokyo. From 2009, he served as the manager of the Jet Engine Technology Research Center, then as the manager of the Propulsion Systems Research Group at JAXA’s Institute of Aeronautical Technology. He was appointed to his current position in January 2015.
[ Mar. 23, 2015 ]