World's First Loading Arm for Ship-to-Shore Transfer of
Liquefied Hydrogen Developed
April 18, 2019 (JST)
Tokyo Boeki Engineering, Ltd.
Kawasaki Heavy Industries, Ltd.
Japan Aerospace Exploration Agency
Japan Ship Technology Research Association
Tokyo, April 18, 2019 ― Tokyo Boeki Engineering, Ltd. (TEN, President: Hideshige Tsubouchi), Kawasaki Heavy Industries, Ltd. (Kawasaki, President: Yoshinori Kanehana), Japan Aerospace Exploration Agency (JAXA, President: Hiroshi Yamakawa), and Japan Ship Technology Research Association (JSTRA, Chairman: Seiichi Tanaka) announced today that they have developed the world's first loading arm for transferring liquefied hydrogen (LH2) from a carrier to an on-shore storage facility, as part of the Cross-ministerial Strategic Innovation Promotion Program (SIP)* led by the Cabinet Office of Japan.
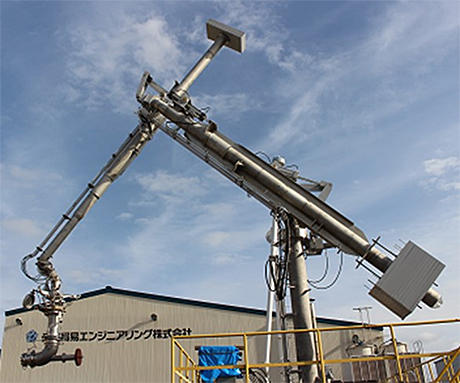
The newly-developed loading arm
Hydrogen has been attracting global attention as an energy source that releases no CO2 when used, just as solar, wind, and other renewable energies do not. Various initiatives are underway to broaden its applications, such as fuel cell cars and hydrogen power generation. Against such a backdrop, Japan has committed itself to achieving low-cost utilization of hydrogen. One such initiative has been construction of an ocean-going LH2 carrier and a handling terminal needed in order to build a global hydrogen supply chain by which mass procurement and distribution of hydrogen will be possible. When completed, the supply chain will provide hydrogen produced from renewable energies, as well as from unused energy resources available outside Japan which integrate CCS (carbon dioxide capture and storage) into the hydrogen production process.
Because marine transport of LH2 by a dedicated carrier is unprecedented, the four organizations have developed one of the key components for connecting carriers and on-shore terminals ― a loading arm for LH2 transfer. Since the temperature of LH2 is lower than the liquefaction temperature of air, using loading arms which were designed for liquefied natural gas (LNG) and developed based on earlier technology would run the risk of fire, because during LH2 transfer, liquid oxygen (LO2) may be generated on piping surfaces. To prevent such generation, a structural design has been developed that provides high thermal insulation performance and ensures safety.
Following are the three key features of this loading arm:
-
1.
A double-walled vacuum insulation structure that provides high thermal insulation performance
By providing a vacuum between the outer and inner pipes, a high level of insulation is achieved, maintaining the surface temperature of the outer pipe at close to the ambient temperature and precluding LO2 generation. -
2.
A highly-flexible swivel joint for the piping that permits 360-degree rotation while maintaining high thermal insulation
This joint enables piping to be used in ways which do not compromise the double-walled vacuum insulation feature. It also accommodates various berthing positions and/or movement of the vessel, and at the same time achieves a tight seal that prevents hydrogen ― a tiny molecule ― from leaking. -
3.
An emergency release system (ERS) that safely interrupts LH2 transfer in the event of an emergency
An ERS is incorporated in the loading arm to respond to emergency situations such as earthquakes or tsunamis during LH2 transfer by quickly shutting the valves of the pipes and safely disconnecting them from each other so that the carrier can leave shore immediately.
The loading arm was developed jointly by TEN, which possesses expertise in developing and manufacturing LNG loading arms, and Kawasaki, which has seasoned experience in manufacturing LH2-related equipment and systems, with JSTRA acting as development project leader, utilizing its extensive research on various marine vessel technologies.
The swivel joints and ERS which are signature to this loading arm went through a series of LH2 performance verification tests at Noshiro Rocket Testing Center in Akita Prefecture, Japan, which is operated by JAXA, an aerospace research and development institute with ample knowledge of LH2 as a rocket fuel. The tests involved disconnecting the ERS filled with LH2, as well as 400,000 sequential rotations of the swivel joint, to ensure a high level of safety and durability over time.
The ERS developed here will be applied to a demonstration project regarding marine transport of LH2 ― "The Demonstration Project for Establishment of Mass Hydrogen Marine Transportation Supply Chain Derived from Unused Brown Coal" ― subsidized by the New Energy and Industrial Technology Development Organization (NEDO). To advance the utilization of hydrogen and realize a sustainable society, we will be focusing on the establishment of international standards for the loading arm in view of its commercialization in the future, and on the development of an upgraded version with larger capacity.
Specifications for the loading arm:
Arm length | : 11.5 m |
---|---|
Base riser height | : 5.5 m |
Material (plumbing) | : Stainless steel |
Structure (plumbing) | : Double-walled vacuum insulation. The outer pipe withstands external forces and the internal pipe maintains internal pressure. |
Main components | : Arm driving system, swivel joints, emergency release system (ERS) |
*The Cross-ministerial Strategic Innovation Promotion Program (SIP) is a national project led by the Cabinet Office for achieving scientific and technological innovations. This development project was conducted between October 2014 and March 2019 as one of the themed projects under the "Energy Carrier" program of SIP, entitled "Development of Cargo Loading/unloading System for Liquefied Hydrogen and the Relevant Rules for Operation."