Industry’s First Technology to Use Magnesium Alloys in Wire-Laser Metal 3D Printer Developed by Multi-sector Consortium in Japan
Mitsubishi Electric, Kumamoto University, Tohokinzoku and JAXA pave the way for producing lightweight, fuel-saving industrial components with highly processable magnesium alloys
June 13, 2024 (JST)
Japan Aerospace Exploration Agency
Mitsubishi Electric Corporation
Kumamoto University
TOHO KINZOKU CO., LTD.
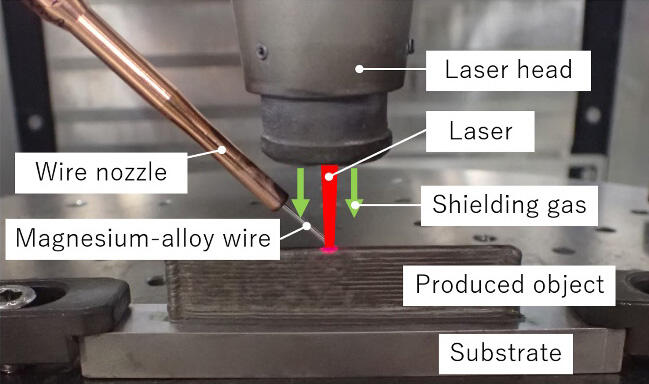
Magnesium-alloy additive manufacturing system
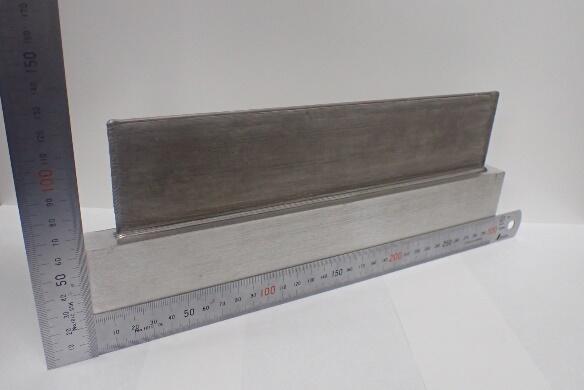
Sample of magnesium alloy for additive manufacturing
TOKYO, June 13, 2024 – Mitsubishi Electric Corporation (TOKYO: 6503), Magnesium Research Center (MRC) of Kumamoto University, TOHO KINZOKU CO., LTD., and the Japan Aerospace Exploration Agency (JAXA) announced today the 3D printing industry’s first*1 high-precision additive manufacturing (AM) technology for using magnesium alloys in a wire-laser metal 3D printer via the directed energy deposition (DED)*2 method, marking a significant leap forward in industrial manufacturing. Unlocking the potential to process magnesium alloys with unparalleled precision and complexity will pave the way for rocket, automobile, aircraft, etc. components that are lighter and stronger than those made of iron or aluminum, leading to improved fuel efficiency and, in the case of rockets, reduced production costs. In addition, the envisioned production processes based on a wire-laser metal 3D printer will be more energy efficient and generate fewer greenhouse gas emissions compared to conventional processes, promising to deliver low-impact solutions for increased sustainability.
Since September 2022, the consortium members have been conducting joint research (Research on Laser Wire DED Method AM Process Technology Using Magnesium Alloy Wire) under the framework of JAXA’s Innovative Future Space Transport System Research and Development Program,*3working to reduce the weight of rockets and thereby drastically cut costs. In addition to rockets, the need for weight reduction has increased in recent years due to factors including the shift to electric vehicles and the growing demand for commercial aircraft, so magnesium alloys are attracting attention in many fields. But magnesium alloys are typically processed by die casting,*4 making it difficult to create structures with hollow interiors. Also the mainstream powder bed fusion (PBF)*5 method for AM, which uses heat to selectively melt metal powder, can lead to degradation through oxidation or dust explosions, posing a problem for safe manufacturing.
In response, the consortium combined Mitsubishi Electric's metal 3D printer, which uses the wire-laser DED method and metal wire instead of metal powder as a material, with a highly nonflammable KUMADAI heat-resistant magnesium alloy*6 developed by MRC. In tests, Mitsubishi Electric repeated the molding process with the KUMADAI heat-resistant magnesium alloy produced by TOHO KINZOKU using advanced wire drawing technology. The result is a new technology that uses a magnesium-alloy wire as an AM material and precise temperature control to prevent combustion.
Based on JAXA’s evaluation of AM production samples produced with this new technology, it is estimated that some rocket parts could be made up to about 20% lighter than those with traditional aluminum alloy structures.
Furthermore, it is believed that the same process could be widely applied to other fields where weight reduction is also required, including various transportation equipment and robotic components. Accordingly, further research and development targeting applications in various industrial fields will be conducted in parallel with Mitsubishi Electric’s work to commercialize the technology in a wire-laser DED metal 3D printer by around 2029.
Product Features
- 1) AM of magnesium-alloy wire combines high workability and strength
- - MRC studied many KUMADAI heat-resistant magnesium alloys to find a composition for AM that is flame-resistant even in wire form.
- - TOHO KINZOKU established a technology for producing wire of any diameter and length for AM, and fabricated prototype wires that were extensively tested by Mitsubishi Electric, resulting in an optimum wire thickness and wire drawing process.
- 2) High-precision AM technology uses nonflammable magnesium-alloy wire
- - Mitsubishi Electric has developed a technology for its wire laser DED metal 3D printer that precisely controls laser power and wire speed using computer numerical control (CNC) to keep the processing area at a constant temperature. This enables magnesium alloys with a width of 3mm to be processed into any shape with high precision and without burning.
- - Unlike die casting, no mold is required, eliminating the cost of changing and replacing molds.
- Magnesium-alloy AM structure will lead to lighter rocket parts
- - AM production samples achieve a high tensile strength of about 250 megapascals (MPa) at room temperature and about 220MPa at high temperatures around 200 degrees, equal to or better than conventional methods. Also, the samples have been shown to be heat resistant and nonflammable.
- - In evaluating the samples’ applicability as rocket materials compared to conventional materials, JAXA found that the weight of rocket shell structures and aerodynamic control fins could be significantly reduced by up to 20%.
- 4) AM processing does not generate greenhouse gases, supporting sustainability
- - Magnesium alloys are lighter and stronger than aluminum and iron, so their use in automotive and aircraft components will contribute to greater fuel efficiency.
- - Compared to machining from ingots,*7 minimized material waste will help improve energy efficiency in processing as well as conserve materials.
- - The technology eliminates the use of sulfur hexafluoride (SF6), a greenhouse gas with a high global warming potential that is conventionally used as a shielding gas*8 for magnesium-alloy casting, helping to significantly reduce greenhouse gas emissions.
Purpose of the Joint Research
The aim of this joint research is to commercialize a new alloy wire material for metal AM that has superior strength compared to existing alloy wires, in order to realize drastic cost reductions of rocket structures through the weight reduction of large structures such as propellant tanks. High-strength wires suitable for metal AM can be applied not only to space transportation, but also to various transportation equipment and robot components where weight reduction is required, as well as other ground structures.
Responsibilities of Each Consortium Member
Mitsubishi Electric | Mitsubishi Electric Development of AM technology using magnesium alloys and verification of material properties of AM production samples |
MRC | Selection of magnesium-alloy composition for AM |
TOHO KINZOKU | Development of manufacturing method for magnesium-alloy wire |
JAXA | Evaluation of magnesium-alloy AM production samples to estimate potential impact on rocket weight reduction |
*1 According to Mitsubishi Electric research as of June 13, 2024 *2 AM process that uses thermal energy to fuse materials as they are being deposited *3 Innovative Future Space Transport System Research and Development Program.
https://www.kenkai.jaxa.jp/eng/research/kakushinyusou/kakushinyusou.html *4 Metal casting process that forces molten metal under high pressure into a mold cavity *5 AM process where a thermal energy source, such as a laser or electron beam, selectively fuses regions of a powder bed to form a solid part *6 Magnesium alloy developed by MRC that achieves superior strength and heat resistance *7 Block of pure material, often metal, that is cast into a shape for further processing *8 Gas used to prevent molten magnesium from igniting when exposed to air
Related Links
- Research and Development Directorate
- Mitsubishi Electric CorporationExternal Link
- Kumamoto UniversityExternal Link